200223 製造現場の問題解析手法(ヒストグラムの利用と対策紹介)
今回は「製造現場の問題解析手法」というテーマで話をします。
生産工程がどの程度安定しているかを示す指標に「工程能力」というものがあります。生産技術エンジニアであれば知っている内容になりますが、意外と実践できている人は少ない印象です。課題を解決する上では役に立つ内容なので今回取り上げてみました。
【目次】
- 工程能力とは
- 工程能力調査(ヒストグラム)の活用事例紹介
- 具体例紹介1(規格中心と分布中心が一致していない場合)
- 具体例紹介2(規格設定に対して実力がない場合)
- 具体例紹介3(異常分布の場合)
- 工程能力とヒストグラムのメリット
工程能力とは
工程がどの程度安定しているかを示す指標です。
ここでは細かい計算式は省略しますが、規格幅に対して標準偏差がどう分布しているかを示す指標になります。工程能力が十分でないと、その工程は不良品を作ってしまう不安定な工程ということになります。
マネジメントレビューでの判断指標の1つにもなっていて、新規生産ラインをリリースするときには、全工程にわたって工程能力調査を行います。特に「特殊特性」と呼ばれる重要特性(機能特性や安全特性)については工程能力1.67必達になります。
また、顧客に対して工程変更申請をするときにも変更前後の工程能力評価は必要項目になります。
以上が一般的な工程能力の紹介です。
上述したイベントの時を除いて、普段の日常業務においても有用なのですが、なぜか日常業務では有効活用しない人が大勢います。例えば不良率を改善したい場合も工程能力調査は有効な分析手法です。不良の分布が異常なのかどうかを調べることができるからです。
工程能力調査(ヒストグラム)の活用事例紹介
細かい説明に入る前に、ヒストグラムの紹介をします。
ヒストグラムとはデータの分布をグラフにしたものです。「工程能力」の問題を可視化する上では大変便利です。
※エクセル操作でヒストグラムを作成できます。詳しくはエクセルのアドイン機能を追加して作成してみてください。
ヒストグラムの見るポイントは次の2つです。
1)規格の中央値と分布の中心の位置関係
2)分布の末端と規格上下限の位置関係
以下の参考事例でこの関係を説明しています。
具体例紹介1(規格中心と分布中心が一致していない場合)
まず1つ目の事例です。
以下ヒストグラムに示す通り、正規分布しているにもかかわらず、規格幅に対して余裕がない場合です。
上述した見るべきポイントの
1)については、規格の中心と分布の中心が一致していません。
2)については、分布が上限規格に対して余裕がありません。
したがって、このまま生産を続けるといずれ上限を超えた不良品が発生します。
取るべき対策は2つです。
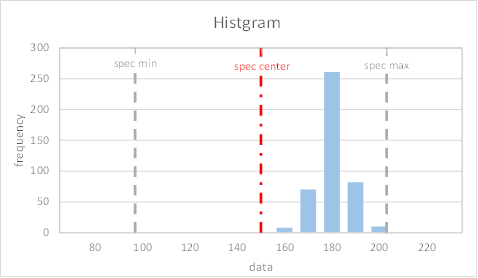
対策A)工程内のパラメータを調整して分布の中心を規格中心にシフトさせる
「圧入寸法」のような事例です。
例えば、圧入寸法の規格が90.0±0.1㎜だったとします。
現状の分布中心が90.07㎜で規格上限に近い場合は、圧入位置を調整して90.00付近にすれば工程能力は大きく改善します。
こうすることでヒストグラムは次のようになります。規格上限に対して余裕ができたので安定した工程になります。
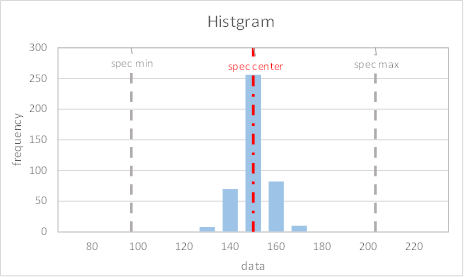
対策B) 規格設定を変更する
一方で、工程内ではデータ分布を調整できない場合です。
「圧入荷重」のような事例です。
この場合は、製品設計側で規格変更してもらうしかありません。
例えば、圧入荷重規格が1000~3000Nだとして、現状の分布中心が2800Nである場合は、部品の公差を見直してもらうか、規格設定を見直してもらうしかありません。工程上ではどうしようもならない問題です。
規格変更後のヒストグラムはこのようになります。
この方法でも、規格上限に対して余裕ができ安定した工程になります。
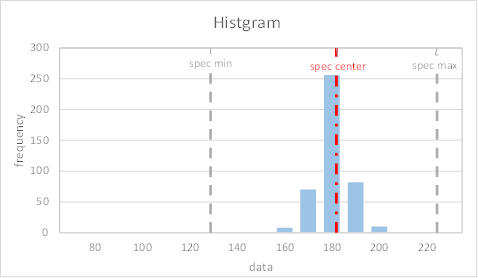
具体例紹介2(規格設定に対して実力がない場合)
次は2つ目の事例を見ていきます。
同じようにポイントを分析すると、
1)については規格の中心と分布の中心はほぼ一致しているので問題ありません。
2)については規格上下のいずれに対しても余裕がありません。
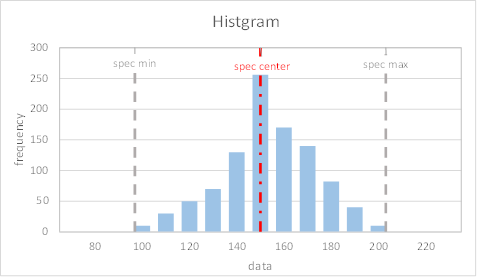
この場合は、規格設定に問題がありますので、規格緩和してもらうしかありません。
規格緩和後のヒストグラムは次のようになります。
これで規格上下限のいずれに対しても余裕が生まれます。
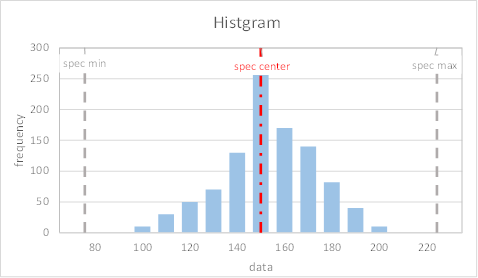
具体例紹介3(異常分布の場合)
3つ目の事例です。
ヒストグラムに赤矢印で示しているデータは、完全に異常分布しているデータです。
こういった不良の場合は、工程内の異常あるいは部品単体での異常が考えられます。
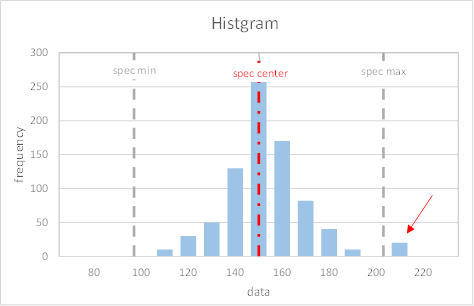
工程能力とヒストグラムのメリット
このように、工程能力やヒストグラムを使用することで問題を可視化することができます。
正しい手法を学んで、うまく使いこなすことができれば、原因調査をすることで少しずつ課題が明確になります。
上述したように、工程内で解決できる課題や工程内で解決できない課題があります。
それぞれの場合に対して、採用するべき方法は変わってきます。
また、場合によっては製品特性(電気特性や機能特性)にかかわる工程能力もあります。
この場合は、FTA分析(別記事参照)をおこない複合的な原因調査が必要になります。
製品構造や特性についても深く理解していないと、正しいアプローチが難しくなります。
※関連記事) 圧入荷重を正しく計測するためのロードセルの取り付け位置
※関連記事) 製造現場の不良率改善とパレート図の利用についての概略説明
※関連記事) 製造現場の問題解析手法(FTAの概略紹介と利用法)