200414 気密性試験の概要紹介と生産技術者が気付きにくい盲点
今回は「気密性試験の概要紹介と気付きにくい盲点」というテーマで話をします。気密試験の概略紹介、量産設備での気密試験の実施方法、生産技術エンジニアをしていて実際にあった失敗事例を紹介します。
気密性(シール性)試験とは
気密性試験とは製品の気密性(シール性)を検証する方法で、一般的にはシールしたい部分に空気で圧力をかけて、そこから漏れた空気の量を測定してシール性を判定しています。
自動車等に使用される電子部品は雨水などの侵入による製品の故障を避けるために、制御機器には高い気密性(シール性)を持たせています。防水性の電気製品(例えばデジタルカメラなど)は、このシール性を確保しているため水に濡れても故障しない構造になっています。
工場での生産ラインではすべての製品を水没して検査するわけにもいかないため、水の代わりに空気を使用してシール性を検査しています。一方で信頼性試験などの実験室での試験では、実際の使用環境を想定して水没試験が実施されます。
量産工程での気密性(シール性)試験の構造紹介
少し図を使って説明します。
下図は簡単な概略図になりますが、量産工程では、製品のシールしたい部分にウレタンやゴムなどの伸縮性のある材料を押し付けた状態で固定します。(ステップ1)
その後、リークテスターから圧力をかけます。一定時間待って配管内の圧力が上昇した後に配管内の体積変化をもとにリーク量を算出します。(ステップ2)
※この計算はリークテスター内部で実施されます。
以上が検査フローになります。
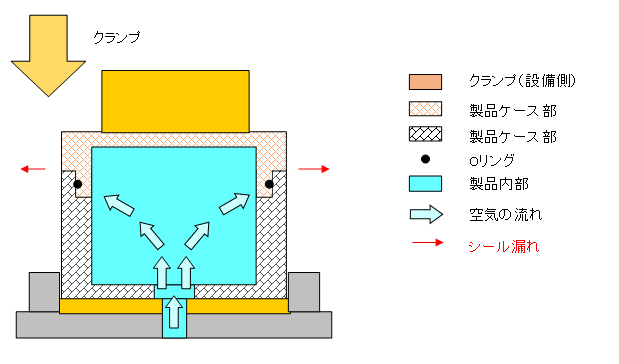
※絵心がなくてすみません
概略図で描いていますが、精密機器は基本的にはこの構造です。
内部を組み立てたあとにケースで蓋をするという構造です。端子やコネクタなどの通電部周辺が外にむき出しになっています。
設備側の注意事項
簡単な検査ですが、少し注意点を紹介します。
ワンタッチ継ぎ手や膨張性のあるチューブは避けるべきです。
いずれも加圧時に配管内部の体積が膨張するため、判定結果が安定しません。
継ぎ手部分はねじ固定式の剛性のあるものを利用し、配管に使用するチューブはテフロン製などの硬度があるチューブを利用します。
※これは設備仕様を準備するときにも重要な要素になります。
こういった基本要求事項を理解しないエンジニアが準備した設備仕様や設備では、設備が完成した後で期待した精度が得られないといったことが起こります。
気密性試験での失敗事例
これは以前担当していた製品でのエピソードです。
その製品の外郭は2つのアルミダイカスト部品でできていました(ちょうど上に図示したような構造です)。シール性を高めるために合わせ面に挿入したOリング周辺にグリスを塗布していました。
※気密性(シール性)を持たせるためには、指定の寸法公差で2つの部品を組み付けなくてはなりません。ところが、そのまま組み付けると組み付け時にOリングが擦り切れてしまうため、外周にグリスを塗布するという方法が一般的です。またグリスがシール性を助けています。
量産ラインを立ち上げてひと段落した時でした。
PVサンプルの信頼性試験をした結果、気密不良品が見つかったのです。全数量産ラインで気密性検査をして合格しているにもかかわらずです。そこで調べたところ、装置のクランプがシール性を補助していることが分かりました。
先述の構造のように、工程内でのクランプが2部品のシール性を補助する方向に働くため、クランプのやり方によっては気密試験に有利になるのです。一方で信頼性の水没試験では、端子周辺部のネジ穴を使用してシールしていました(カバーを抑えつけるクランプではありませんでした)。この違いのために、信頼性試験ではわずかな漏れが検出されたのです。
この問題は、量産工程ではどうしようもない問題でした。その製品形状ではクランプしないで気密試験をする方法などなかったからです。幸いにも実際の製品の使用環境も量産工程と同様の構造でクランプされた状態であることから、大きな問題にはなりませんでした。
いづれにしても大きな発見と学びがあった出来事でした。
気密試験自体は簡単な構造のため、正しく検査できていると考えていたのですが、実際には見落としがあったのです。
以上、簡単ですが気密性試験の概略と失敗事例を紹介しました。