200321 抵抗溶接の概要紹介(パラメータ検証~安定稼働まで)
今回は「抵抗溶接の概要紹介」というテーマで話をします。生産技術をしていると、様々な工法を利用します。そのなかでも製品通電部分の接合に利用される抵抗溶接について、生産技術エンジニアの経験をもとに、初期のパラメータ検証のやり方や量産時の注意点を中心に説明します。
なお、溶接という工法は使用する場所や目的によって、管理項目が大きく変わります。品質的に重要でない部分の溶接であれば、細かい管理は不要です。今回は、通電部分の金属接合に溶接を導入するという前提条件で話をします。通電部位の接合は、極めて高いレベルの品質基準が求められます。
【目次】
- 抵抗溶接とは
- 金属同士の接合方法の紹介
- 抵抗溶接の初期評価
- 溶接パラメータ評価
- 溶接状態の品質評価
- 抵抗溶接工程の品質における注意点
- 量産での抵抗溶接工程の懸念事項
- 端子の形状
- 電極の発熱
- 溶接電極の耐久性と溶接電極の品質
- 電極コスト
1.抵抗溶接とは
抵抗溶接の原理は、図に示すように金属端子を電極で挟んで加圧した状態で、大電流を流して接触部の抵抗により発熱を加えます。その状態で加圧することで金属端子を溶かして固定するという工法です。
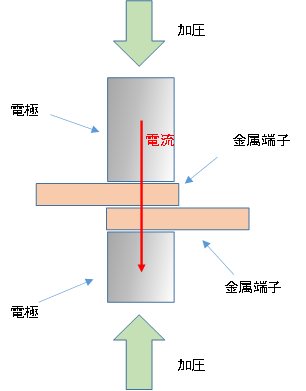
2.金属同士の接合方法の紹介
金属同士の接合には、抵抗溶接の他にもアーク溶接(一般的に溶接と聞いてイメージする溶接です)、圧入、カシメ、半田などがあります。それぞれメリットとデメリットがあります。
通電部位でない部分の金属の接合には、機械的な接合だけを求める圧入やカシメが使用されます。これらは溶接や半田に比べて工法もシンプルで、品質管理が簡単です。
一方、通電部位は成形された金属端子の形状が多く、一般的に機械的強度がありません。こういった部分には溶接や半田が使用されます。アーク溶接は落雷の原理で金属を溶かすため、細かい管理が難しく、電極の耐久性もありません。半田については、工法自体は簡単ですが、半田ボールが混入するリスクがあることと、高温状態での信頼性に課題があります。
そういった背景から、通電部の接合に抵抗溶接は使用されます。
3.抵抗溶接の初期評価
ここからが生産技術の仕事内容になりますが、導入する前には初期評価をしなくてはなりません。試作段階でのサンプル生産の前に溶接パラメータ評価を行います。これは量産工程でも同様です。量産設備が完成した後には、生産開始前に再度検証を行います。
製品の使用環境にもよりますが、高温状態での通電部の耐久性や外部衝撃に対する強度を保証するためには、ただ接合されていて導通があればよいということではないからです。
さらに、通電部位などの機能に関わる部分の品質については特殊特性になっていることが多く、通常の品質よりも高いレベルの管理が要求されます。そしてその管理基準を決めるのは生産技術エンジニアになります。
検証項目は次の内容になります。
たくさんの項目があるので、具体例を挙げながら説明します。
<パラメータ評価項目>
加圧力、溶接電流、溶接時間、変位量、溶接電極
<品質判断項目>
溶接強度、断面カット
溶接パラメータ評価
加圧力を3種類ほど選定します。
金属端子のサイズや形状などをもとに、溶接機器のメーカーにあたりをつけてもらうか、類似機種のパラメータを参考にすればよいです。それぞれの加圧力で、溶接電流と溶接時間で以下のようなマトリックス評価を行います。どのあたりの条件が安定しているかというざっくりの見極めを行います。
※以下のマトリクスでは青をOK、赤をNGとしています。
このときの判断項目は変位量と溶接外観です。
変位量の判断基準は後程記載します。
溶接外観については、溶け具合と溶接強度の関係をもとに決定してください。
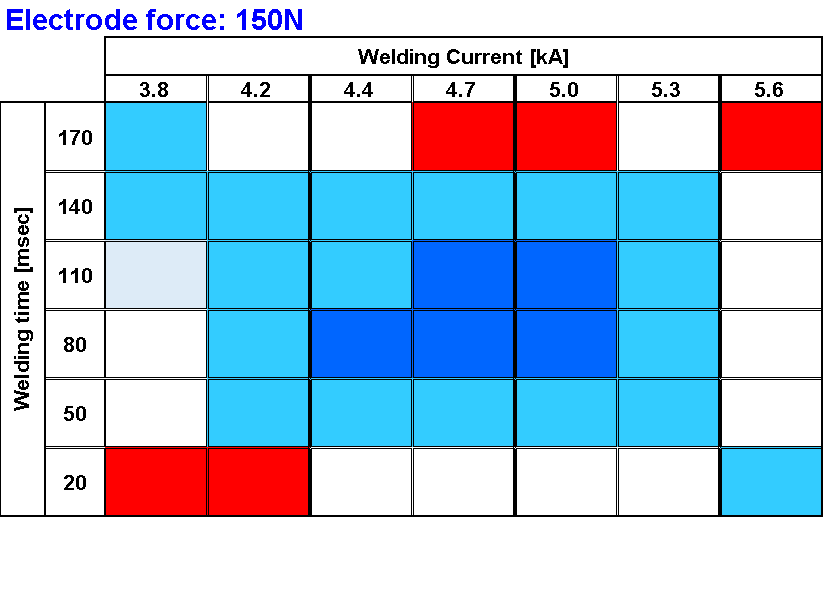
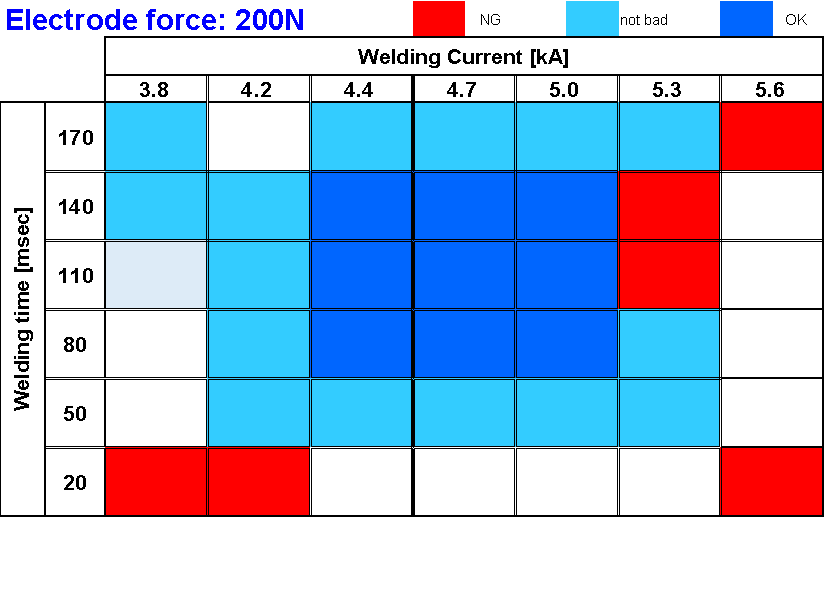
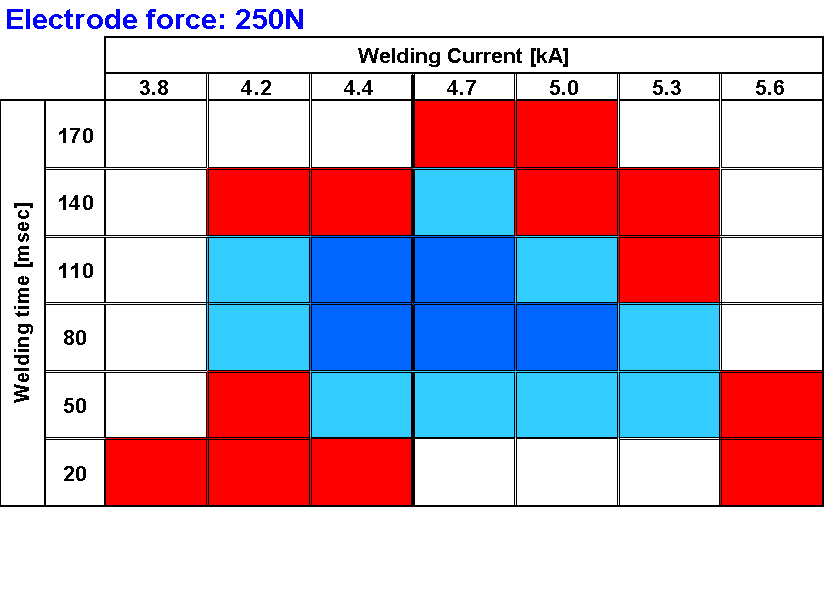
安定範囲が広いパラメータが確保できる加圧力で、さらに細かい調査を行います。
上の例でいえば、加圧力200Nとした場合の安定領域が広いので加圧力を200Nとして、青色の領域で詳細パラメータを決めていきます。
溶接状態の品質評価
続いて品質評価です。溶接条件ごとに作成したサンプルの溶接強度を測定します。
その溶接強度と変位量の関係をグラフに表します。
グラフのように、変位量が増えるにつれ溶接強度は増えていき、ある点まで来ると溶接強度に変化はなくなります。
この状態を超えて変位量を増やすと、溶接強度は下がっていきます。イメージしやすいかと思いますが、この溶接強度下がったポイントは溶かし過ぎているということです。
端子の接合の安全率を考慮しつつ、電極への負荷や耐久性を考慮すると、適度な溶接状態は変位量0.5~1.0㎜の部分ということになります。
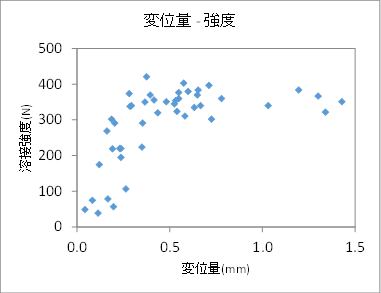
これで、溶接条件は決まりました。
この後は、同一パラメータで連続してサンプルを作成し、変位量と溶接強度の工程能力評価を行います。工程能力に問題なければ、これで初期評価完了になります。時間のかかる面倒な仕事になりますが、生産技術エンジニアの仕事範疇になります。
抵抗溶接工程の品質における注意点
溶接や半田という工程は出来栄えを定量的に判断しにくい工程になります。圧入や検査工程のようにスペックがあって数値判断できるようなものではありません。溶接外観と溶接電極の変位量という間接的な判断材料のみになります。(溶接部の破壊強度検査や断面カットのように、溶接部を破壊すれば直接品質を確認できますが、あくまで抜き取りでしかできません)
したがって、溶接時の工程パラメータの信頼性が品質を大きく作用します。この事実を正しく理解しておかないと、量産時に重大な品質問題をおこします。
4.量産での抵抗溶接工程の懸念事項
つづいて量産工程でのポイントについて解説していきます。
初期の検証では想定していない問題が量産時には発生するもので、その時の事例をいくつか紹介します。
端子の形状
抵抗溶接を安定させるポイントの1つに端子形状があります。平面同士の接合であれば比較的安定していますが、一方が球面などの形状をしていると電極との接触部の安定という点では不利になります。この形状が、電極表面の消耗を早めたり、接触抵抗が不安定になって変位量が不安定になるといった問題を引き起こします。
端子形状は製品設計部が設計する製品形状次第ですが、製品開発部の担当者は溶接のことなど知らないので、生産技術エンジニアが情報をインプットしておく必要があります。必要に応じて初期の段階で端子形状の提案をしておくべきです。
電極の発熱
連続使用していると電極が発熱し、電極内部の抵抗が溶接動作に影響します。
冷却チラーなどを使用して量産工程に対応しますが、連続使用状況により採用すべき冷却能力は変わるため、冷却能力については正しく見極めておく必要があります。
冷却能力が不足している場合は、溶接側の品質にも影響しますが、冷却チラー側でアラームがあがり、量産になりません。こういうことは意外と起こります。初期の段階は生産数が少ないので問題に気付きにくいのですが、本格稼働した後に実は能力が不足していたというようなことがよくあります。
溶接電極の耐久性と溶接電極の品質
続いて溶接電極の耐久性と品質です。
使用頻度にもよりますが、本格稼働すると1日に数回は交換したり電極表面を磨いたりすることになります。電極品質が良くない場合は、電極交換後に溶接が安定しないという問題が発生します。初期評価の時点では同一の電極を使用していたため、量産まで見つからなかった問題が電極を交換すると出てきます。
溶接電極は、タングステンと銅で作成されています。電極内部のタングステンと銅の接触状態や抵抗によっては、抵抗溶接の動作に影響を与えます。
電極コスト
最後に電極コストです。
上述したように1日に何度も交換していると地味に費用が発生します。電極単価を下げておくことが長期的に大きな効果を生んでくれます。おもに電極形状などの初期の検討ですべてが決まります。値段のかからない形状を提案しておく、あるいは類似機種での溶接電極が転用できるのであれば、その電極の兼用するという案を初期の時点で採用しておくことです。
以上、抵抗溶接について初期評価から量産までのポイントになります。
生産技術者の視点でまとめています。
※関連記事 TIG溶接の原理と量産工程での課題の紹介