200326 TIG溶接の原理と量産工程での課題の紹介
今回は「TIG溶接の原理と量産工程での課題の紹介」というテーマで話をします。生産技術エンジニアの経験をもとに、TIG溶接の概要や量産時の注意点を中心に説明します。TIG溶接は昔からある技術で導入コストは安いのですが、量産工程に適していない部分があることも事実です。
【目次】
- TIG溶接を使用する用途と背景
- TIG溶接の原理
- TIG溶接のメリットとデメリット
- TIG溶接の初期評価と管理方法
- 溶接のパラメータ検証
- 溶接後の品質管理項目
- 量産工程での懸念点
- 電極の耐久性について
- 電極交換によるサイクルタイムへの影響
- 失火問題
- ショート問題
- ノイズ対策
- シールドガスの準備
TIG溶接を使用する用途と背景
抵抗溶接記事でも紹介しましたが、金属同士の接合には溶接、圧入、カシメ、半田などがあります。通電部位でない部分の金属の接合には、機械的な接合だけを求める圧入やカシメが使用されます。これらは溶接に比べて工法もシンプルで、品質管理が簡単です。
圧入やカシメが利用できない接合箇所や高温状態での強度が要求される部分は溶接が利用されます。但し、TIG溶接は落雷の原理で金属を溶かすため、細かい管理が難しく、電極の耐久性もありません。
TIG溶接の原理
TIG溶接の概略はシールドガスで溶接部を空気と遮蔽した状態で行います。これは溶接部の酸化による劣化を防ぐためです。図の要領で電極に電圧をかけて、雷の原理で電極先端から放電します。
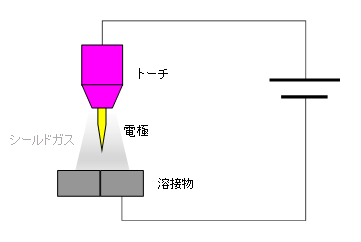
模式図では平面の金属板として描いていますが、電界の集中を考えると平面よりも先端が尖った形状がTIG溶接には適しています。
TIG溶接のメリットとデメリット
TIG溶接を利用するメリットはスペースの制約が少ないことです。狭いエリアにも電極先端が侵入できるため、狭い部分の接合には適しています。また、技術自体も以前からあるもので導入コストも安いというメリットもあります。レーザー等の接合方法を利用する場合は1桁高い導入費用が必要になります。
一方でデメリットをあげると、耐久性がないことです。連続使用すればわかりますが、電極先端を鋭利な状態にしておく必要があるため、電極先端の消耗が溶接の品質に影響してきます。電極研磨用のグラインダーで頻繁に電極を研磨する必要があります。また溶接位置の管理が困難というデメリットもあります。先述した通り、落雷の原理で溶接位置が決まるため、どの位置を溶接するかという予測が簡単ではありません。
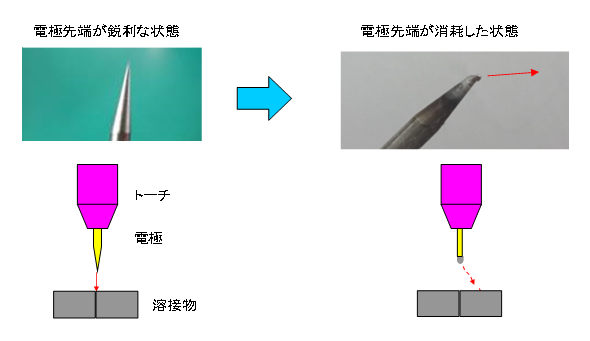
TIG溶接の初期評価と管理方法
溶接個所によりますが、ただの剛体の固定であれば溶接後の強度を満足させるだけの保証になります。端子と銅線などの導通部分を溶接する場合は、溶接外観、溶接後の電気特性、周辺部の耐圧特性(絶縁が破壊されていないかどうか)などを保証する必要があります。 生産技術エンジニアが注目すべきポイントは次の項目になります。
溶接のパラメータ検証
溶接条件の評価方法は抵抗溶接記事で紹介した内容と同じになります。主なパラメータは、溶接時間、溶接電流、電極と溶接物の距離などになります。
溶接後の品質管理項目
品質判断項目は、溶接個所によりますが、溶接外観、溶接強度、溶接後の電気特性、周辺部の耐圧特性(絶縁特性)などになります。また、溶接スパッタと呼ばれる溶接飛散物が周辺に飛び散る可能性もあるため、金属不純物が発生してほしくない場所を溶接するときにはそういったスパッタの有無の外観確認も必要になります。
量産工程での懸念点
それでは以上を踏まえて、生産技術エンジニアが量産で注意すべきポイントを紹介していきます。
電極の耐久性について
電極先端の角度や電極先端と溶接物の距離などをいろいろ検証したことがあります。そのときの結果では、電極先端は先端角度15度くらいの鋭利な形状で、すり減ったら押し出して連続使用する方がトータルで考えるとロスが少ないという結果になりました。
※ただし、やりすぎると逆に位置調整で失敗してダウンタイムが増えることになります。
交換した方のメリットが大きいか、電極を押し出し続ける方のメリットが大きいかは装置構造や経験則によります。
電極交換によるサイクルタイムへの影響
1サイクルでの溶接回数にもよりますが、この電極交換の頻度が多いため、当初想定していたサイクルタイムは悪化します。以前私が使用していた溶接装置では、1時間に1度は電極交換が必要でした。1回の交換作業が3分としても、60分のうち3分の時間は確実に失われます。稼働時間で5%もロスすることになります。
ライン全体で見た時に、この溶接工程がボトルネックになっていなければ、電極交換のロス時間は気にする必要はなくなります。もし溶接機がボトルネック工程であれば、サイクルタイムを短縮する改善を行わない限り、電極交換のロス時間が大きなインパクトを与えることになります。
失火問題
ノイズ対策でノズル内部に金属のメッシュが付属しています。また、セラミックノズル外周にアース線を巻き付けることもノイズ対策として実施していました。いずれも溶接電源メーカー推奨になります。
ショート問題
失火の逆のパターンです。電極先端が溶接物に接触した場合にはアークを飛ばすことができず、溶接エラーになります。このように、電極先端の微妙な位置出しが要求されるのですが、電極先端はすぐに消耗したり異物が付着したりして、その位置関係は失われます。 残念ながら、これがTIG溶接の限界です。
ノイズ対策
これは私が使用した溶接電源の品質が悪かったせいかもしれませんが、溶接電源の誤作動に悩まされました。抵抗溶接機ではノイズによる誤作動を起こすことはありませんでしたが、TIG溶接装置の方は頻繁に失火が起きたり電源エラーが起きたりしていました。溶接電源のマニュアルにも記載がありますが、アース線を別配線したり、トーチやグランド電極配線をノイズシールドしたりしていました。
シールドガスの準備
溶接で消費するシールドガスを供給するため、装置周辺にガスボンベの準備が必要になります。ガスボンベ自体はレンタル可能ですが、なくなる前に交換しないとシールドガスの不測で量産工程が止まってしまうことになります。
ガスボンベの交換を避けたい場合は、工場外に少し大きめのガスタンクを設置してそこから配管を引くことも可能ですが、初期投資はかかります。
以上、生産技術エンジニアの経験からTIG溶接について紹介しました。
※関連記事 抵抗溶接の概要紹介(パラメータ検証~安定稼働まで)