200322 カシメ工法の概要紹介と生産技術者が気付きにくい勘違い
今回は「カシメ工法の概要紹介と生産技術者が気付きにくい勘違い」というテーマで話をします。生産技術をしていると、様々な工法を利用します。生産技術エンジニアの経験をもとに、カシメ工法の紹介や量産時の注意点を中心に説明します。
カシメ工程といっても圧着工具を利用した簡易的なレベルから、油圧プレスやサーボプレスを利用した大規模なものまで存在します。今回扱うのは後者になります。設備の概略でいえば、以下の図のような量産設備をイメージしています。
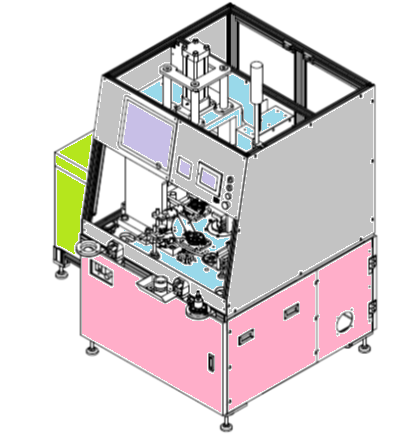
【目次】
- カシメとは
- カシメの正しい制御方法
- カシメの間違った制御方法
- カシメ品質の管理方法
- ストローク管理について
- 量産での懸念点
- カシメツールの摩耗や破損
- カシメ部分の面積
- 量産でのカシメ工法のメリットとデメリット
1.カシメとは
そもそも、カシメとは金属剛体を締結するための工法です。
金属剛体の締結方法は圧入やカシメが一般的で、どちらも似たような工法です。圧入は部品のはめあいを管理した状態で荷重をかけて押し込む工法であるのに対し、カシメは挿入勘合で組み付けたあとに片側の剛体に荷重をかけて変形させて締結させるという工法です。
例えば、ベアリングをアルミハウジングにカシメ固定する場合を考えます。
ベアリングをアルミハウジングに挿入した後に、アルミハウジングの縁をカシメます。
2.カシメの正しい制御方法
カシメの制御方法は一定荷重を一定時間かけて製品を変形させる。
その時の荷重を判定するというものです。その時の荷重グラフは次のようになります。
いたってシンプルです。
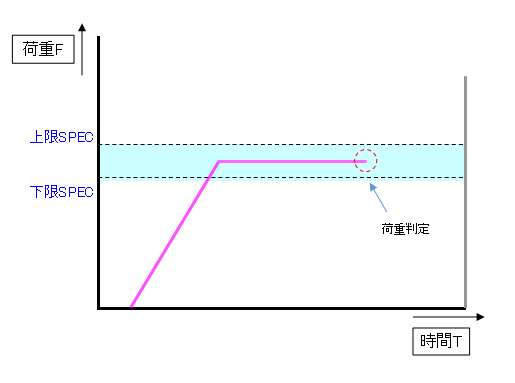
3.カシメの間違った制御方法
まれに、次のような間違った制御をする装置もあります。
ある荷重に到達すると荷重停止して終了する制御方法です。
波形は次のようになります。
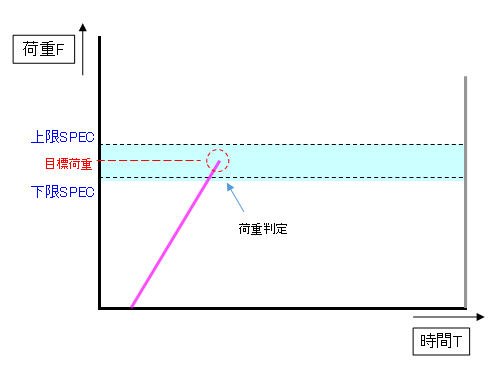
装置の制御はどうにでもなりますので、この制御方法を採用することもできます。ロードセルの荷重到達信号を入力信号として取り込み、プレス動作を止めてしまうという制御です。
問題点として2つあります。
見かけの荷重は正しく表示されているものの、実際の荷重は不明であるということ。
制御機器の応答性によっては、想定以上の荷重が製品にかかっているということです。
例えば、10000Nで止める制御としても、プレスの推力が30000Nで設定されていれば、見かけ上の表示荷重は10000Nになっていたとしても、瞬間的に15000N程度まではかかっている可能性があります。
気付かずにこういう制御を採用している生産技術者は、意外にも大勢います。
4.カシメ品質の管理方法
装置側での判定項目は荷重判定、ストローク判定などです。ただし、これらはあくまで装置の動作判定です。
製品側の品質が正しいかどうかは、装置の判定結果からではわかりません。
製品カシメ部分の外観、カシメの深さ、抜け荷重などは直接製品側を見なければ判断できません。
カシメの目的は部品の締結です。振動や衝撃によって部品の締結力が失われてしまうようなことがあっては、製品の重大な機能不具合になります。どんな製品でも カシメを使用するような部分(部品の締結が要求される部分)は特殊特性になっています。
したがって、通常工程以上の厳しい品質管理が要求されます。
管理図を使用したカシメ深さの管理や、定期的な破壊試験により抜け荷重のモニタリングなどです。
5.ストローク管理について
装置によってはカシメ深さを測定しようと、リニアゲージなどを搭載している装置もあります。どんな測定方法を採用するかによって、寸法の信頼性は大きく変わります。
例えば、リニアゲージをプレスの下に待たせておいて、プレスが下降した時に下降位置を判定するような測定の方法では、ただの参考値にしかなりません。これでは、正しくカシメの深さを測定することは不可能ということです。
セットする製品の高さ方向の公差バラつきの影響を受けるため、カシメの深さは測定できません。測定できるのは、プレスがどの位置まで下がったかという参考値です。
正しくカシメの深さを測定しようとすると、サーボプレスなどを搭載してカシメの荷重がたった座標から最終カシメ位置までのプレスストロークを取り込む必要があります。この場合は、信頼性の高い測定値といえます。
6.量産での懸念点
工法自体がシンプルなので、安定稼働しやすい工程ではあります。
とはいえ、消耗部位であるため日常の品質管理および定期的な交換が必要になります。
また、カシメのツールが変わるとカシメの品質に大きな影響を与える可能性があるためカシメツールの品質には注意が必要です。
カシメツールの摩耗や破損
カシメツールは材料選定や焼き入れ処理で耐久性を持たせてあります。とはいえ、消耗部位になるため定期的な交換対象部品になります。装置にカウンタを搭載してショット数管理をする、あるいはカシメ深さの管理図の推移をもとに管理幅を決定する、定期的な製品の破壊強度の推移を見て交換時期を判断する、などの管理が一般的です。何も管理しないのは危険です。
カシメ部分の面積
カシメツールの接触部分の面積が変わると、同じ設備パラメータでもカシメ品質は変わります。圧力P = 荷重F / 面積S なので分かりますね。プレス荷重が同じでもカシメツールの面積が変われば、最終的な製品への圧力が変わるためです。カシメ跡の面積が増えたり減ったりする結果、カシメの深さが浅くなったり、深くなったりします。
カシメツールの重要部分については、正しく寸法指定されているか図面をよく確認する必要があります。また、予備のツールが完成した時には正しい寸法通りに仕上がっているかどうかもよく確認する必要があります。
7.量産でのカシメ工法のメリットとデメリット
カシメという工法は荷重をかけるだけで2部品の締結ができるため、材料費の面では大きなメリットがあります。カシメを使用しない場合には、ネジやトメワなどの何らかの固定具が追加で必要になります。材料費の面での効果は簡単に想像できますね。工法自体も決して難しくありません。
一方でデメリットを挙げると、1つは分解できないことです。カシメという組立工程は完全に不可逆工程であるため、後で分解しようとしても、破壊しない限り不可能です。例えば、何かの不具合で大量の不良在庫を抱えることになっても、救済する方法はありません。不良率などの面で不安定な製品(分解の可能性が高い製品)には、カシメ工法を採用しない方が良い場合もあります。
もう1つが金属屑の混入リスクです。金属を変形させる工法であるため、動作前後で金属屑を発生させます。また、アルミ製品へのカシメであれば心配は少ないのですが、鉄製品へのカシメの場合にはカシメツールの破損リスクも考慮しておく必要があります。ツールの1部が欠けていても、荷重やストロークで検出できる可能性はゼロに等しく、金属屑が製品に混入するという重大不具合を引き起こす可能性があります。
以上、カシメ工法で生産技術者が注意すべきポイントを紹介しました。
※関連記事 圧入荷重を正しく計測するためのロードセルの取り付け位置