200324 カメラによる画像判定の概要紹介(エッジ検出の原理)
今回は「カメラによる画像判定の概要紹介」というテーマで話をします。生産技術エンジニアの経験をもとに、カメラの画像判定の概略紹介や量産時の注意点を中心に説明します。
【目次】
- カメラによる画像判定の背景
- カメラによる画像判定のメリット
- カメラによる画像判定のデメリット
- 画像判定の原理と機能
- エッジ検出のしくみ
- 量産工程での懸念点
- 複雑なフローを組まないこと
- ソフトの習得が必要ということ
カメラによる画像判定の背景
カメラの価格低下や判定の自動化を背景にカメラによる自動判定を生産ラインに導入する事例は増えています。
私が初めて導入したのは2010年前後でしたが、当時はカメラの画素数も200万画素程度で、ユニットの価格も100万円弱ほどしました。
現在では画素数は2000万画素のものも出てきています。安いカメラであれば、センサの延長くらいの感覚で数万円程度で購入できるようになっています。
余談ですが、10年前もデジタルカメラは数万円程度で販売されていました。同レベルの画素数なのに、産業用のカメラはなぜこんなに高額なんだろうと感じていましたが、高額な理由は、ハードではなくソフトの部分です。
カメラによる画像判定のメリット
カメラのメリットは次のようなものです。
定量的な判断ができる。処理が速い。記録が残る。人が判断する場合に比べてハンドリングも簡単になり、判定者による品質の差はなくなります(品質判断が定量化します)。また、導入コストも下がっているため、作業員を配置するよりもはるかに安いコストで生産ラインを設計できます。
また、画像データを記録として残すことも可能です。最近では画素数が増え、画像データのサイズが大きくなっていますが、NG判定の画像のみを残すという処理も選択可能です。
カメラによる画像判定のデメリット
あまりデメリットは見つからないのですが、あえて挙げるとすれば、微妙な映り方の違いで誤判定を起こすということです。基準位置の形状が微妙に変化したり、検出部に変な光の反射がおこると誤判定してしまいます。人が判定する場合には、影響しなかった些細な事柄でもカメラ判定する場合には、影響してくるということです。
画像判定の原理と機能
画像判定にはいろいろな機能があります。
位置補正、エッジ検出、色抽出、寸法測定、形状判定・・・・など、パソコンと同じ機能を持っていると考えてください。メーカーによって操作性などのソフト仕様は違いますが、基本的な内部処理は同じです。ここではエッジ検出について原理を簡単に紹介します。
エッジ検出のしくみ
画像データはピクセルという多数の点から構成されています。1ピクセルはRGBAという要素から成り立っています。
R(Red、赤)、G(Green、緑)、B(Blue、青)、A(Alpha、透過度 )で、それぞれに1バイト使用されています。たとえば2000万画素のカメラがあったとして、縦5000画素×横4000画素の画素数(ピクセル数)とします。※縦×横で合計2000万の画素数です。
このスクリーンの中のN番目の画素数のRGBAのデータをそれぞれ次のように定義します。
R: data(N+0)
G: data(N+1)
B: data(N+2)
A: data(N+3)
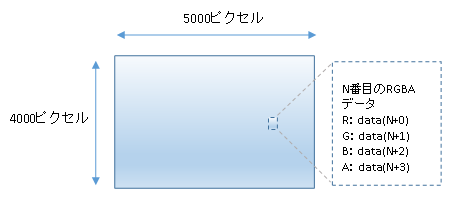
このしくみや処理はパソコンの画像編集ソフトとまったく同じ仕組みです。
N番目のRGBAデータとN+1番目(N番目の隣のピクセル)のRGBAデータを比較して、変化の大きい部分をエッジとして検出します。
検査する方向をそれぞれX軸方向、Y軸方向として、検査方向や向きを決めています。
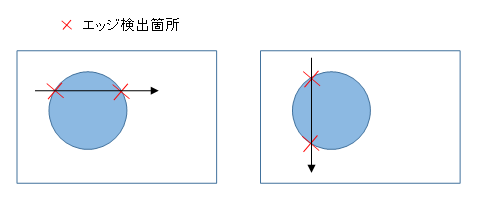
簡単ですが、以上がエッジ検出の原理です。 ( ※参考:
簡易エッジ検出プログラム)
カメラなどのハードの部分は基本的には同じです。ソフトウェアも基本的にはどこの会社も同じですが、このソフトウェアを各社独自開発しているため、市販のデジタルカメラに比べて産業用の画像判定ユニットの価格が高価なものになっています。
量産工程での懸念点
10年以上生産技術の仕事を経験してきたうえでカメラの懸念点を挙げると2つあります。
運用にあたって、ソフトの習得が必要ということと複雑なフローを組まないことです。
複雑なフローを組まないこと
コンピュータの処理速度は一瞬です。1秒もかからない間にすべての画像判定を処理することができます。生産技術者によっては、何でもかんでも検査してしまう場合がありますが、私はこの考えにあまり賛成しません。
例えば、50個くらいのフローを組むことも可能です。エッジ検出だけでなく、位置補正や演算を組み合わせて難解複雑なフローを組んでいる場合もよく見かけます。
ソフトの習得が必要ということ
少ないコストで多数の検査をできるという点ではメリットがありますが、これはソフトのメンテナンスコストを受け持つということを認識しなくてはなりません。製品の量産を終えるまで、導入担当者がその生産ラインの責任を見るのであればよいのですが、そんなことは実際不可能です。24時間の生産体制になれば1名で面倒を見ることも不可能です。
他人が見てわかりにくい制御はできるだけ避けるべきです。機械図面や配線図と違って、ソフト制御は設備の取扱説明書には記載されることは少なく、仮に記載されたとしても内容を理解するのは簡単ではありません。PLCプログラムや配線図と違って、他人があとで見てわかるコメントや全体感がわかる情報がほとんど存在しないというのが私の印象です。検査アルゴリズムを組んだ人間以外は概略を理解することができず、機器の操作方法や検査アルゴリズムを1から分析しないとデバッグできないというのが残念な現状です。つまり、他のエンジニアにとっての最初のハードルがかなり高くなるのです。
同じようなカメラ・画像判定を他の生産ラインと共通化している場合は、このハードルを下げることができます。他ラインとの共通性もなく、最新の商品を盛り込んで導入しただけの新規ラインでは、こういった弊害を引き起こします。
※参考)簡易エッジ検出プログラム
※関連記事)設備構想図のレビューと設備のレイアウト