200426 生産技術エンジニアが理解しておくべき管理図の概略紹介
今回は「生産技術エンジニアが理解しておくべき管理図の概略紹介」というテーマで話をします。生産技術をしていると設備問題や不良改善だけでなく、知識として知っておくべき事柄がたくさんあります。今回は工程管理をする上で大切な管理図の概略と作成のポイントを紹介します。
管理図とは
管理図にはいろいろな種類がありますが、今回は使用頻度の多いX-R管理図について紹介します。
管理図とは、工程のバラツキを統計的に監視するための手法です。特殊特性などの重要工程の管理で使用される手法で、統計的な傾向を分析することで異常を早期に発見するためのツールです。
通常の製品規格や設備判定規格とは別に、新たに設置した管理幅(UCL,LCL)を決めてその管理幅の中で運用する手法です。
生産技術エンジニアにありがちな失敗事例
製造現場ではいたって一般的なツールですが、製造現場で働く製造部責任者や生産技術部のエキスパートを除き、私がこれまで見てきた生産技術エンジニアの中では大半の人が管理図の理解が浅く、製造現場でつけているシートくらいにしか認識していないようでした。
具体的には次のような状況です。
- そもそも何のために管理図があるかを理解していない
- 新しい管理図の作成ができない
- 異常傾向を判断できない
管理図の作成手順
それでは管理図の作成方法を簡単に紹介します。
内容さえ理解していればいたって簡単です。
1.サンプルデータを準備する。
(目安:サンプルサイズ5個程度のサブグループ20~25からなるデータ100個程度)
※部品ロットや生産時間などをまたぐサブグループでのデータ収集推奨
2.平均値Xと範囲Rを算出する
まず、サブグループごとの平均値と範囲を算出し、そのあとに全体での平均値Xと範囲Rを算出します。
3.UCLとLCLを決定する。
※細かい計算方法は省略します
4.管理図のフォーマットに平均値X、範囲R、UCL、LCLを記入する
全体的な流れは、上記のようになります。
管理図作成のメイン業務は1と2の作業です。このデータさえあれば、8割は完成したも同然です。
1.2の概略が分かるサンプルを添付します。
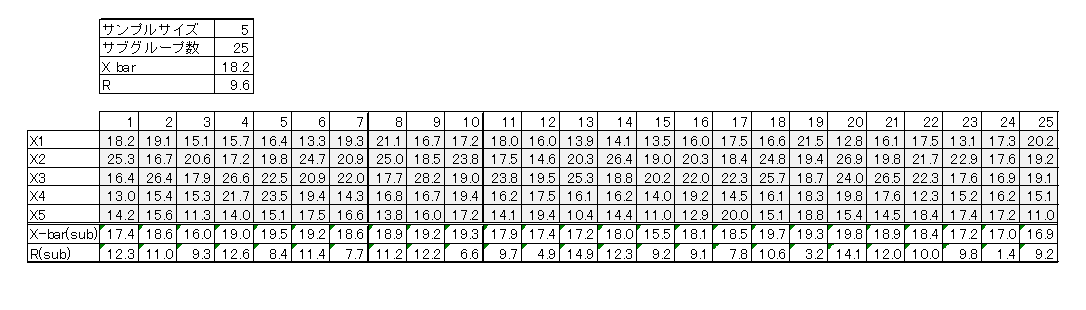
管理図のポイント
注目すべきポイント(異常傾向)
- 異常傾向1:管理限界線(LCL,UCL)を超える
- 異常傾向2:中心線の片側に連続して7つの点(連)がある
- 異常傾向3:連続して増加または減少する7つの点(連)がある
- 異常傾向4:管理限界幅の中央1/3の範囲内の点が、その他2/3の点数よりはるかに多い
- 異常傾向5:管理限界幅の中央1/3の範囲内の点が、その他2/3の点数よりはるかに少ない
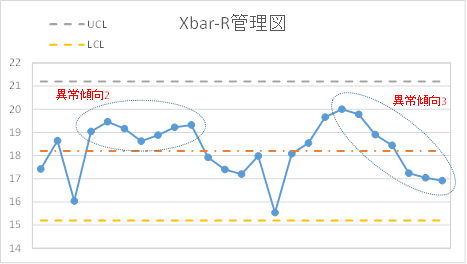
イメージ的に異常傾向1を異常と認識している生産技術エンジニアは大勢いましたが、それ以外の傾向については理解が浅いという印象です。普段の仕事で管理図を利用する機会は少なく、業務上の支障はないのかもしれませんが、仕事上で当然知っておくべき事柄になります。
意図的に学ぶ努力をしなければ、いつまでたっても理解できるようにはなりません。
製造現場のレベルによっては管理図を用いて統計管理を行っていないようなこともあります。
正しく運用できていない場合は、顧客監査などでは間違いなく指摘される項目になります。意地悪な監査員であれば、管理図の管理方法自体を理解しているかどうかを質問してきます。
なかには管理図を記載している掲示板のわきに、管理図の異常傾向を掲示している会社もありました。こうすれば、わざわざ現場人員を教育しなくても、いつでもカンペがあるので自然に異常傾向が何かを覚えてくれます。
以上、簡単ですが管理図の概略を紹介しました。
参考書籍) 図解 IATF 16949 よくわかるコアツール【第2版】
※関連記事 製造現場のマネージメントとスキルマップの概略紹