200329 製造業界における製品トレーサビリティの概略紹介
今回は「製造業界における製品トレーサビリティの概略紹介」というテーマで話をします。生産技術エンジニアをしていると、生産ラインの維持と改善がどれほど大変かということを実感するようになります。その理由の1つに、出荷した製品の品質を保証しなくてはならないという制約があるからです(ただ作ればいいという考えではなく、大きな責任を伴う状況で生産維持するということは大変作業です)。今回はその概要を紹介します。
【目次】
- 製造業界における出荷製品へのメーカー責任
- 一般的な製品トレーサビリティ方法の紹介
- レベル1 帳票管理(完全な手作業による記録)
- レベル2 データ管理(検査工程のみシリアル管理)
- レベル3 データ管理(ほぼ全工程にわたりシリアル管理)
- DMC(DataMatrixCode)のメリットと導入コスト
- DMC導入の概算コストとスキャナの読み取り精度
- DMC読み取り異常を起こす要因
- 阻害要因1 ハレーション
- 阻害要因2 余白の欠如
- 阻害要因3 素材の表面状態
製造業界における出荷製品へのメーカー責任
製造業界では、PL法といって出荷製品に対する品質責任を製造元に課しています。市場へ出荷した製品に重大な品質欠陥があった場合の品質責任は、製造元になります。品質問題を隠すこともできませんし、欠陥が見つかった場合は該当商品の回収責任や代替品の出荷責任を伴います。
会社によっては、事業拡大やマーケットシェアの拡大を目指していますが、それらはすべて品質維持が前提になります。品質レベルが低く、市場クレームのリスクを抱えると、事業拡大により会社をつぶしてしまうリスクが生まれるからです。市場への出荷が増えるほど、市場クレームを起こした時の補償範囲が大きくなるということです。
以上の理由から、製造業界のメーカー各社は出荷した製品の品質保証および欠陥品の絞り込みができる仕組み(製品トレーサビリティ)を採用しています。
一般的な製品トレーサビリティ方法の紹介
簡単に生産工程を紹介します。
部品の投入、組立、検査、出荷という流れです。
この時の重要なパラメータは、部品、設備、人です。
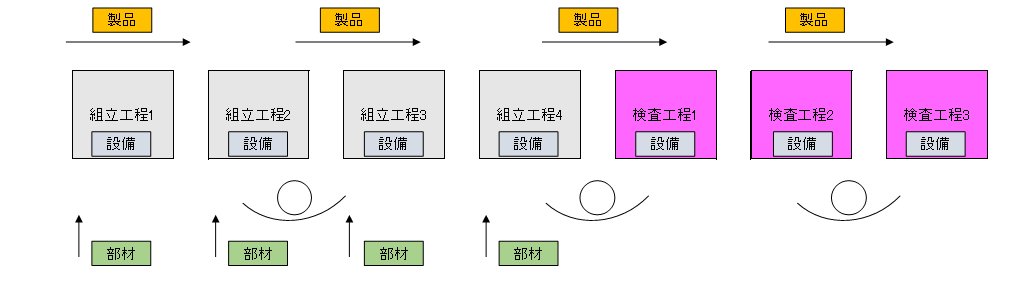
続いて、どういった方法で製品トレーサビリティを実施しているか紹介します。
大きく分けて3種類あります。それぞれ導入コストと絞り込みの点でメリットとデメリットがあります。また取り扱う製品によっても向き不向きがあります。
レベル1 帳票管理(完全な手作業による記録)
いわゆる4Mと呼ばれる要素の管理です。
- 生産日の担当作業員の記録
- 設備の点検記録
- 初品の品質記録
- 使用した部材のロット記録
これらを、ドキュメントに毎日記録し、そのドキュメントを保管するというものです。
このトレーサビリティ方法は導入コストがかからないというメリットがあり、以前から各社が採用している一般的な方法になります。
ところがデメリットもあります。毎日記録する必要があり、その保存量は膨大になるということです。自動車業界では製品製造後10~15年の品質文書の保管を要求しています(※期間は取引顧客の要求により若干前後しますが最低でも10年です)。
問題発生時に過去の記録をさかのぼるにしても、検索作業も自動化することができません。該当文書が見つからないなどという可能性も出てきます。仮に文書をPDFなどに電子化するにしても、その追加工数が生まれます。
ということで、簡単に導入はできるものの使い勝手は悪く、長期的には適していません。
レベル2 データ管理(検査工程のみシリアル管理)
つづいて2つ目のトレーサビリティ方法を紹介します。こちらは半自動化した場合です。
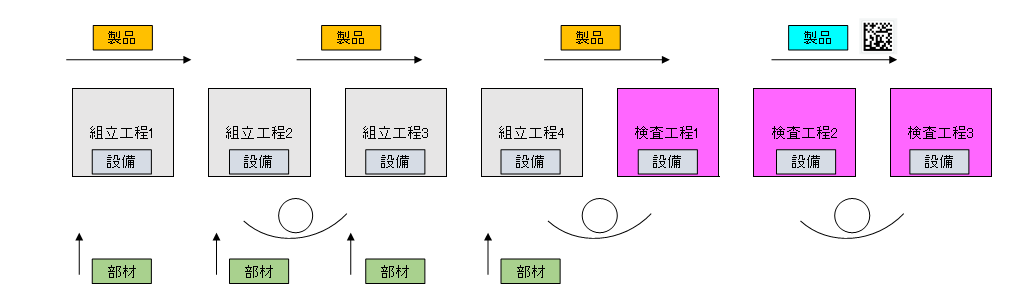
図のように最終製品にDMC(DataMatrixCode)を追加しています。DMCがあれば、製品ごとの個別の検査データを管理可能になります。顧客要求による場合もあれば、社内的な理由でDMCをつける場合もあります。DMCとは簡単に言えば、製品のシリアルです。例えば、以下のDMCには"200329A0300001"という情報を入れてあります。
参考)QRコードの発行はコチラ
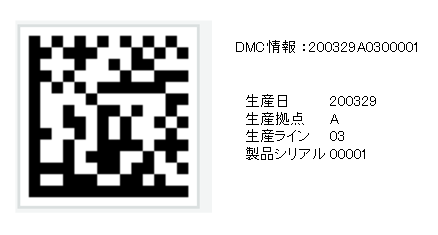
例えば、生産日、製品シリアル、生産ライン番号、拠点番号などが分かるシリアルにしておけば、そのシリアルを見れば生産日と生産場所を特定することができます。
また、この製品シリアルと設備の検査データを一緒に保存しておけば、全数の検査結果を後で調べることも可能になります。
レベル1に比べて、問題発生時の記録検索、照合作業の負荷を大きく減らすことができます。また、検査データを処理すれば統計的な分析も即座に可能になります。
レベル3 データ管理(ほぼ全工程にわたりシリアル管理)
つづいてレベル2のDMC管理を全工程に適応した場合を紹介します。イメージは次のようになります。最終製品ではなく部品レベルからDMCを適応します。
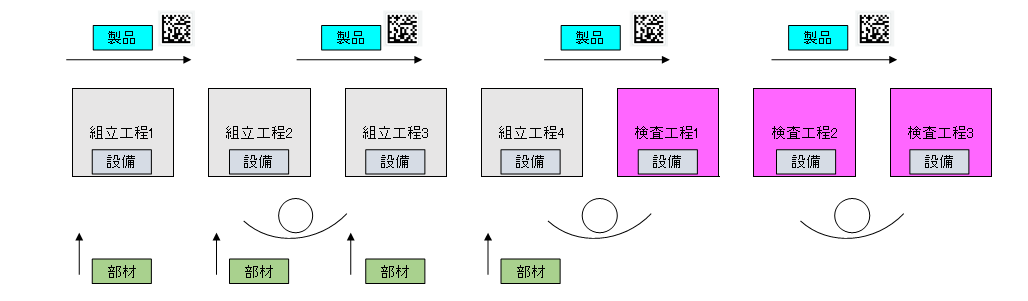
こうなると、品質管理を自動化できる対象範囲が増えます。また部材ロットをDMC情報と一緒にデータ保存することもできるようになるため、製品検査データに追加して投入部材の情報もシリアル情報と管理することが可能になります。
レベル1に比べてたくさんのメリットがありますが、この案にもデメリットはあります。それは導入コストが大きいということです。ハードの面でいえば、DMCスキャナの購入、サーバーの準備です。ソフトの面でいえば、サーバー環境の構築とそのメンテナンスです。
初期投資がかかる上に、そのメンテナンスにも対応できるように人材を教育しなくてはなりません。また、「途中からデータが保存されていなかった」というような事態を避けなくてはならないため、サーバーへのデータ保存に異常があった場合には生産ラインに自動でフィードバックがかかるような仕組みを準備しておく必要があります。
こうなると、データ保存異常による生産ライン停止といった問題が発生します。設備に異常がなくても、製品品質に異常がなくても、自社のデータ管理の都合だけで生産ラインを止めてしまう可能性が出てくるということです。生産技術者なら、この行為がどれほどもったいない行為かわかるはずです。
DMC(DataMatrixCode)のメリットと導入コスト
最後にDMCの概略を紹介します。
生産ラインに導入すると、レベル1、レベル2で紹介した理由から、生産技術者の仕事の面でいろいろ便利になります。ただし、DMCを追加したことによる弊害があることも事実です。
例えば、上述した「ネットワーク異常で生産ラインが止まった」場合と同じように、「DMCが読み取りできないから生産ラインが止まった」というライン停止が発生します。DMCがなければ生産ラインが止まることはなかったことを考えると、もったいないロスです。
DMC導入の概算コストとスキャナの読み取り精度
DMCの刻印にはレーザーマーカーが使用されます。メーカーによりますが、概算価格は200~400万円です。長年、生産技術者をやってきましたが、あまりレーザーマーカーの故障経験はなく10年近く使用できていた機器がほとんどでした。
DMCのスキャナについては安いものであれば5万円程度です。高いものであれば20~30万円するものもあります。DMCスキャナを安くできるかどうかは、DMCの読み取りやすさです。面積の狭い部分に刻印する場合や曲面に刻印する場合は、高精度のスキャナを利用しなくてはなりません。それ以外の場合は、数万円程度のスキャナで対応可能です。
DMC読み取り異常を起こす要因
いくつかDMCの読み取りを阻害する要因を紹介します。
阻害要因1 ハレーション
まずはハレーションと呼ばれるものです。カメラを扱ったことのあるエンジニアであれば分かると思いますが、照射した光の反射によってDMCの一部が白飛びしてしまうことです。こうなるとスキャナが正しくDMCを認識できません。
対策としては、スキャナの角度を調整することです。ただし、曲面に刻印されたDMCの場合はこのハレーションを避けることが極めて難しくなります。DMCは平面に刻印することを勧めます。
阻害要因2 余白の欠如
つづいて余白の欠如です。DMCの周辺に白字の余白があります。白字ですが、これはDMCを正しく認識するための重要な部分になります。製品の刻印スペースに余裕が少なく、位置ずれなどによりこの余白が切れてしまうようなことが起きると、読み取りエラーを引き起こします。
刻印する位置を決めるときには十分な余白を確保してみてください。
阻害要因3 素材の表面状態
つづいて素材の表面です。アルミダイキャスト品などは問題にならないのですが、鉄などの金属の加工品やプレス品は洗浄後の洗浄液の変色や熱処理時の変色により、表面状態が微妙に変化することがあります。 ところが、製品設計者はDMC刻印のことなど気にしないため、表面状態の規定をしていません(そもそも量産前のサンプル生産段階でDMCを導入することなども少ないため、問題として出てきません)。ところが、量産が始まるとこういった部品バラつきの影響がもろに発生します。この問題はサプライヤと取り決めをして解決していくしかありません。
以上、製造業界のトレーサビリティについての概略紹介でした。
※関連記事 製造業における量産の恐ろしさ
※関連記事 過剰な品質検査は機能しない。大切なのは〇〇です。