200406 製造現場の不良率改善とパレート図の利用についての概略説明
今回は「製造現場の不良率改善とパレート図の利用についての概略説明」というテーマで話をします。生産技術エンジニアをしていると、必ず不良率の改善活動という業務に関わることになります。生産技術の経験をもとに、不良率の改善方法の考え方の概略を紹介します。
製造現場の不良率とは
本題に入る前に、まず製造業界の現状を簡単に紹介します。
私が過去に勤めていた業界では、新製品の不良率は5~10%程度で、何年も量産している量産機種でも不良率は1%でした。ここでの不良率の定義は次のようにします。
(不良率)=(不良廃却金額)/(その生産ラインでの生産数×製品金額)
つまり、廃却金額/(売上金額+廃却金額)です。
なぜこう定義するかというと、組み立てラインの先頭工程で単価の安い部品レベルでたくさん不良が出ても、不良数は増えるにもかかわらず収益上の影響度は低く、一方で最終製品状態での不良であれば、不良数の数は少ないにもかかわらず収益上のインパクトが大きくなるからです。経営的なインパクトを分かりやすくするために、ここではこのように定義します。
要するに、新機種では廃却金額換算で5~10%を占めるということです。
製造現場の不良率が高い理由
一般の人からすれば、なぜそんなに高いのかと驚くかも知れません。
新機種の場合は、量産して初めて出てくる問題がたくさんあります。これは製品設計上の問題、量産設備の問題、作業ミスの問題、部品品質の問題など原因は多岐にわたります。実験室で数台の製品を作成するのと、毎日数千台の製品を生産するのでは管理レベルの違いをイメージできるはずです。
ということで、新製品の初期の立ち上がりはどうしても不良率は高くなってしまいます。
一方、何年も量産している製品であっても不良率を0にすることは並大抵の苦労ではありません。最終的に残るのは慢性要因の不良になります。どうしても一定の割合で避けられない不良項目というものが、どこの量産工程でも存在します。
設計的な問題もあれば、工程内の問題や部品品質の問題もあります。いずれの場合も、ひとたび量産がスタートすると、製品設計変更、設備改造、部品の仕様変更などはリスク(およびコスト、手間)を伴うため現実的ではありません。対応可能な範囲で計画的に実施することになりますが、それでも半年程度の期間を必要とします。
前置きが長くなりましたが、ここからが不良率の話になります。
不良率と不良項目の整理
不良率の改善活動を始めるにあたって、まずは不良内容の調査から始まります。
生産数、不良項目、不良項目ごとの不良廃却数から不良率をまとめていき、これを日付ごとに整理します。
慢性的に発生している不良と突発的に発生した不良を分けていきます。対策すべきなのは、効果の高い慢性不良です。
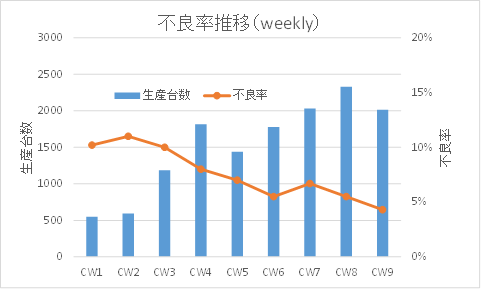
パレート図の紹介
つづいて、不良項目を不良率の高い順にパレート図にしていきます。
※ここでの不良率は工程ごとの(不良数/投入数)で構いません。
以下のようなイメージになります。資料作りが目的ではありませんので、細かい不良項目はまとめて「その他」でOKです。
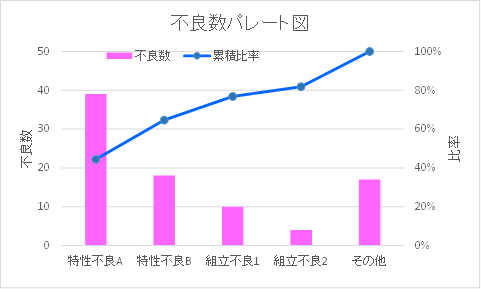
パレート図の効果的な利用方法
パレート図の整理ができたあとは、不良率の高いものから優先的に活動を進めていきます。
いきなり全部の項目を対応することはできませんので、2つか3つの不良項目に絞って活動を進めていきます。それ以外の不良項目はいったん無視します。
説明するまでもありませんが、社内のリソースは限られています。課題解決は、そう簡単には進みません。これは会社経営と同じ考え方ですが、どこにリソースを集中して成果を上げるかという考え方になります。(もちろん可能であれば、全部の対策をすることが理想です)
不良率の改善の考え方
ここまでできれば、あとは具体的な活動に落とし込んでいくだけです。
できれば具体例を挙げて説明したいのですが、あまり個別事例を記載しても、参考にはならないと思いますので記載を控えます。
製造現場の不良改善で全く同じ事例などほとんど存在せず、不良案件ごとに詳細調査して対策することになります。
一方で、あまりに抽象的な説明過ぎてもわかりにくいと思いますので、考え方の参考となるように過去の記事のリンクを貼っておきます。
必要に応じて以下参照下さい。
ヒストグラムの事例
ロードセルの事例
TIG溶接の事例
不良改善のポイントは、しつこく原因を調べることです。
時間はかかりますが、少しずつ傾向をつかんで仮説を検証していく作業になります。数週間という単位で調査・対策検討が必要な場合もあります。数日間やって何も結果が出ないと感じるかもしれませんが、落胆したり、自信を失うようなことはありません。
すでに大勢のエンジニアが挑戦してきて解決できなかった問題の対応をしているのだから、そう簡単に解決できなくて当然です。
以上、製造現場の不良率削減活動の考え方とパレート分析の概略について紹介しました。
※関連記事) 製造現場の問題解析手法(ヒストグラムの利用と対策紹介)
※関連記事) 製造現場の問題解析手法(FTAの概略紹介と利用法)